KIT develops new process to speed up electrode coating for batteries
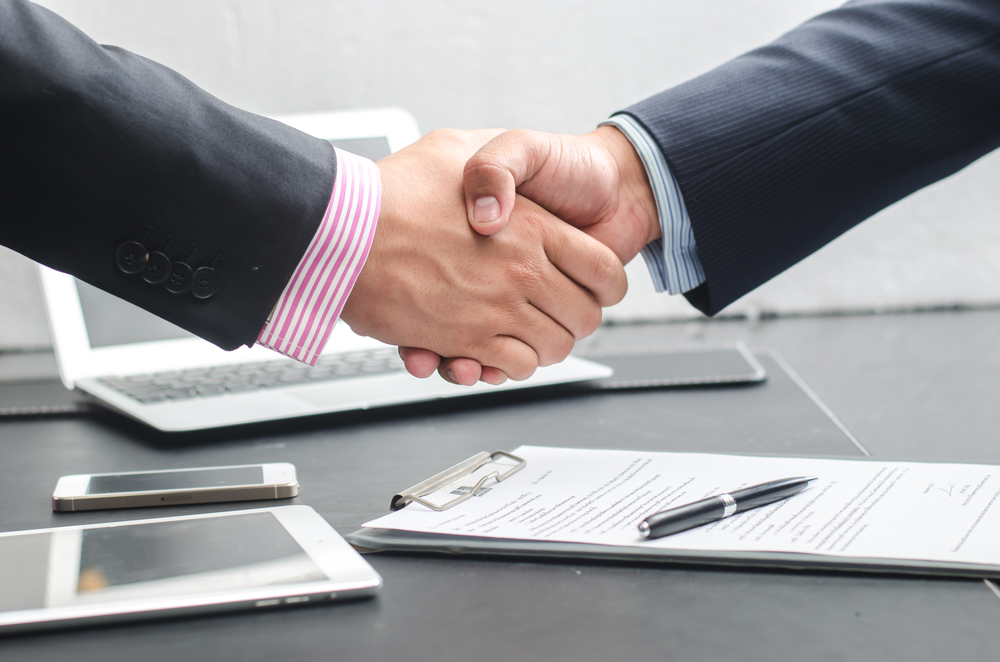
With a new coating process, researchers of Karlsruhe Institute of Technology (KIT) have produced electrodes for lithium-ion batteries at record speed. At the same time, the new process improves the quality of electrodes and reduces production costs.
When producing electrodes for batteries, electrode material in the form of a thin paste is applied to a copper or aluminium foil in a rectangular pattern. The pattern is interrupted by short sections of uncoated foil, which are needed for electron discharge. To produce these sections, the coating process has to be interrupted and restarted repeatedly. A special challenge consists in producing sharp edges without smearing of material at maximum production speeds.
“Precision of electrode coating is an essential factor for efficiency and costs of battery cell production,” said Professor Wilhelm Schabel from the Institute of Thermal Process Engineering – Thin Film Technology (TVT-TFT), who is responsible for research into this topic at KIT. “Even smallest production errors make battery cells unusable. Due to the high reject rate and the low throughput, lithium-ion batteries today are more expensive than actually necessary.” According to Schabel, it is this area where highest cost reductions in cell production are possible.
Doctoral researcher Ralf Diehm, who works in Schabel’s team, has now succeeded in making decisive progress. He optimised the nozzle for the electrode material and equipped it with an oscillating membrane that cyclically stops and restarts the application of the coating paste.
“This membrane is much lighter than mechanical valves, as a result of which quick reaction times and high speeds can be reached,” Diehm said. “So far, manufacturing speeds have been limited to about 30 to 40 metres per minute. With the new technology, we reach up to 150 metres per minute in electrode coating.”
Absence of some formerly used mechanical components in the nozzle does not only increase production speed, it also results in other advantages in electrode production: as the membrane can be controlled more precisely than mechanical valves, production quality is improved and the reject rate is reduced. The technology will now be developed to industrial maturity by a spinoff established by Ralf Diehm and his team.
For entire battery production to profit from quicker electrode coating, the production process has to be readjusted at another point, explained Dr. Philip Scharfer, Head of the Thin Film Technology (TFT) group of KIT, who has studied this topic with Professor Schabel for some years now. “Quicker coating requires shorter drying times. Otherwise, the drying section and, hence, the complete plant would have to be enlarged.”
Based on fundamental studies of different drying conditions, the drying process has already been optimised in a knowledge-based way. As a result, drying time was reduced by about 40% with electrode properties being maintained. Within the ProZell II Research Cluster funded by the Federal Ministry of Education and Research (BMBF), this work is now planned to be continued in cooperation with partners from Technische Universität Braunschweig and the Centre for Solar Energy and Hydrogen Research Baden-Württemberg (ZSW), Ulm.
Electrode production at a record speed and high production quality considerably reduces costs of cell production. On a typical production line, electrodes can be produced for three times as many battery cells, thus meeting the growing need for electric mobility. TFT develops its technologies for electrode production and for future new material systems as part of the Centre for Electrochemical Energy Storage Ulm & Karlsruhe (CELEST), one of the biggest research platforms in the area of battery research worldwide. New findings relating to production technology will also be incorporated directly in the Post Lithium Storage (POLiS) Cluster of Excellence, within which KIT develops batteries for the future together with Ulm University.
KIT develops new process to speed up electrode coating for batteries
Modified on Tuesday 6th August 2019
Find all articles related to:
KIT develops new process to speed up electrode coating for batteries